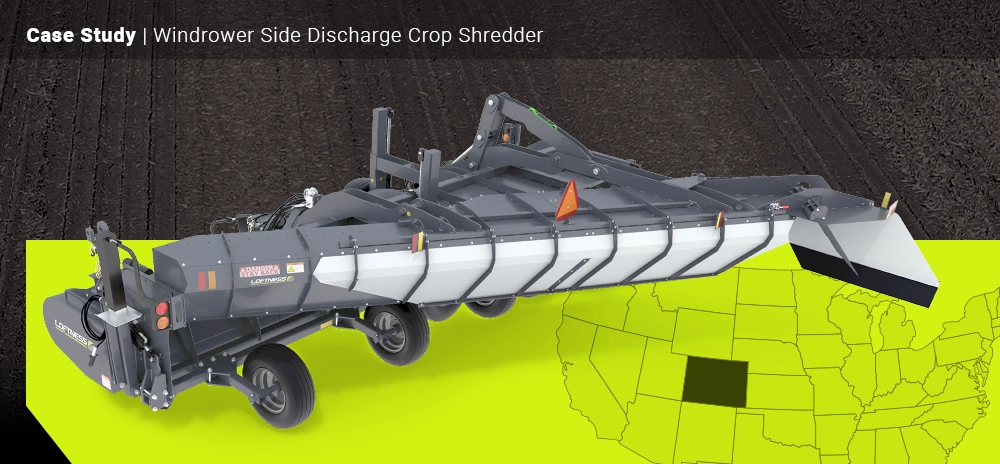
The Background
Located in western Colorado, Derek Frigetto operates a farm and two feedlots in Montrose and Olathe. In 2006 he got into custom haying, covering a nearly 40-mile radius, as nobody else offered the service in the valley. The custom work included baling corn stalks for other area farmers, who wanted the bales for bedding and feed rations in their own livestock operations.
Customer
Derek Frigetto, custom baling operator | Western Colorado
The Basics
Frigetto has more than doubled production, while reducing maintenance problems, by switching brands and using Loftness’ new windrower design.
The Problem
When Frigetto began custom baling, he started with a 15-foot-wide end-delivery flail windrower. This allowed him to place two windrows side by side and bale two passes at a time without having to rake windrows together.
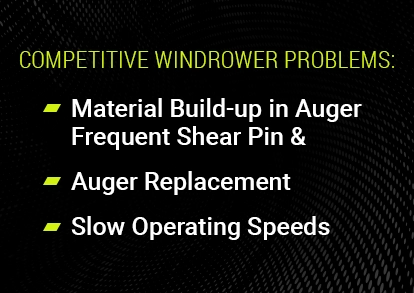
Unfortunately, he encountered numerous issues with his windrower, especially relating to the auger that conveyed shredded material to the discharge. “We were having problems with rocks and dirt building up at the bottom of the auger,” said Frigetto. “It would eventually stop the auger and break the shear pin.”
The frequent shear pin replacement wasn’t the only maintenance headache Frigetto experienced. “The auger itself would also wear out and make material build-up even worse, so we’d have to replace it about once per season,” he said. “We were tearing up machines, needing to replace them every couple of years.” Beyond the maintenance issues, the windrower wasn’t maximizing efficiency, despite being able to place windrows side by side. In order to do a nice, clean job, Frigetto found himself limited to travel speeds around 2.2 miles per hour that slowed the entire baling operation. “I wasn’t staying ahead of my baler,” he said.
The Solution
Tired of repeating the same old problems, Frigetto decided to try a Loftness® product instead — the 20-foot-wide Windrower Side Discharge Crop Shredder. Rather than using an auger, belts, or any other mechanical means to convey material, the new Loftness windrower creates a powerful spinning air vortex that carries shredded material to the side discharge. This exclusive design eliminates many of the moving parts known to cause trouble for Frigetto and other farmers.
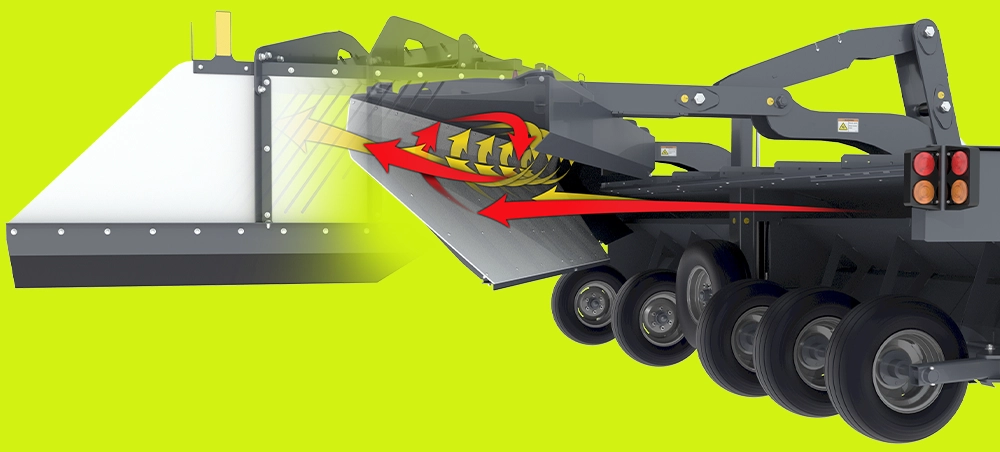
The Results
The Loftness windrower performed as hoped. “The auger on my previous windrower could get overloaded with material, but the Loftness [windrower] doesn’t have that kind of restriction,” said Frigetto. “The cupped knives on the rotor also seem to provide better material flow and higher capacity.”
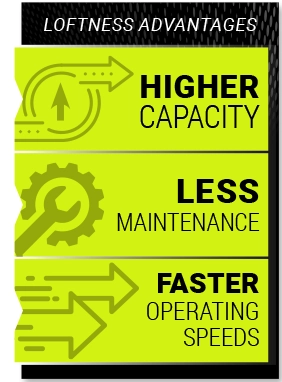
Frigetto experienced multiple benefits from the new design. Most noticeably, the improved flow allows him to operate much faster than the previous machines. “We’re running 6.5 to 7 miles per hour with the Loftness windrower and more than doubling our production,” he said.
In addition to the faster operating speeds, Frigetto feels the Loftness windrower does a better job. The amount of vacuum it produces allows the machine to operate higher off the ground. As a result, rocks have been less of an issue.
He also prefers the condition of the windrow that the Loftness unit produces. “Dirt seems to blow out the top of the machine, so it’s a cleaner product in the end,” said Frigetto. “The windrows also seem taller and less compacted, so they go through the baler easier.” Finally, following years of equipment struggles, Frigetto appreciates having a more reliable windrower. “After running 2,500 acres with the Loftness windrower, the only maintenance we did was to replace about five knives,” he said. “We’re bouncing on furrows all the time, and the Loftness machine seems to have greater strength to handle it. We’ve had no structural problems with it. It’s just heavier duty.”